India a new Synthetic Fiber Hub

Since the development of the first synthetic fiber, i.e., nylon, in the 1930s, Synthetic fibers have been gaining ground. Today, polyester (a type of synthetic fiber) has replaced cotton as the dominant fiber in the market. It is the most widely used synthetic fiber, having risen from accounting for a 37% share of the market in the 2000s to 57% in 2020.
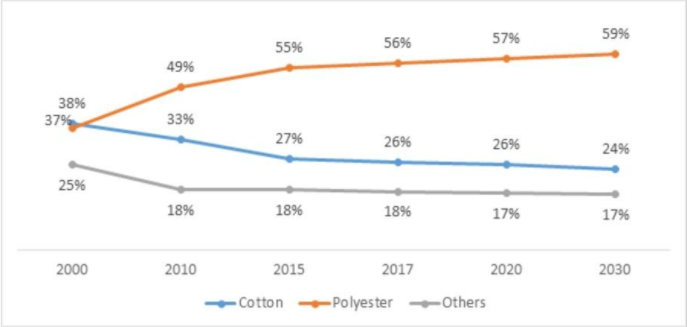
Recycled nylon, viscose, and lyocell are some other synthetic fibres gaining prominence, but polyester by far remains the dominant fibre in the artificial fibre category. It finds numerous applications in sports, fashion, and mass apparel. The cost-effectiveness and adaptability play a significant role in the rapid growth of this fiber. The ability of polyester to combine with other fibres such as Spandex and cotton for specific performance requirements makes it highly versatile. The capability of polyester to be recycled multiple times makes it environment friendly, overcoming a significant drawback among synthetic fibres. Polyester textile recycling has been developed using clear plastic water bottles, or PET, as the raw material, a source of plastic that would otherwise go into landfill.
COVID – 19 Impact
The COVID – 19 crisis has created a sharp hike in demand for protective equipment and masks. Although the synthetic fibre industries have suffered a major setback due to the mass cancellation of orders worldwide, most of them have resorted to PPE production (personal protective equipment) and masks.
Masks made up of cotton and chiffon (primarily based on polyester) as well as cotton and flannel are regarded as promising materials for the prevention of SARS-CoV-2 and are effective at filtering saltwater aerosols. Also, PPE, which is essential for frontline workers, banks heavily on synthetic fibres. It has a shell made from polyester, straps from a thermoplastic elastomer, a filter from polypropylene and the nose from polyurethane.
India’s Standing
Despite massive growth in demand and utility of the synthetic fibres at the global level, India’s domestic production has more or less remained stagnant and, in some cases, declined. China, Japan, South Korea and Taiwan have seized the global markets of synthetic fibres. India’s Man-made fibres production registered a combined annual growth rate of just 0.2% between 2016-17 and 2017-18. Exports declined by 1% during the same period, whereas imports shot up by 16%. China accounted for nearly 49% of the imports in this sector.
By drawing a comparison with the leading players in this industry, we can realize some of the strategies that India needs to adopt to gain a lead in this segment. A considerable amount of investment needs to be made in the research and development of synthetic fibres. Also, synchronization between the industries and academia is of paramount importance to foster meaningful innovation. The level of integration must also be enhanced, which requires a considerable amount of investment and planning. India nearly has no presence of significant players in the high-end segment. Hence, a majority of the high-quality fabric is being imported by India from countries like China, Korea & Taiwan. Production of such categories should be promoted in India. Tapping into FDI thus becomes an imperative strategy for India to gain ground in the synthetic textile market.
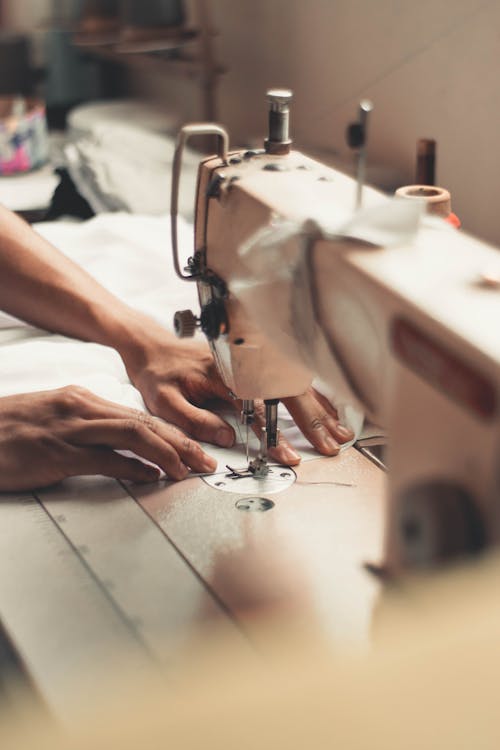
This becomes even more significant as a large number of companies are looking to relocate from China and looking for alternatives. India can project itself as a democratic version of China. The cheap labour, sizeable domestic market, reduced government interference (compared to China) are some of the points that work in favour of India. However, lack of infrastructure, inadequate technical expertise and research facilities and insufficient support from the government (in comparison to China) are some of the thorns in the path of making India a global manufacturing hub.
COVID – 19 Pandemic
India faced a life-threatening shortage of medical masks and personal protective equipment (PPE) needed by health workers at the forefront of the battle against the Covid-19 pandemic. Faced with this medical emergency, many high technology government-owned research institutions threw red tape away and collaborated with the Indian private sector. From almost having nil production facilities of PPE in February, India went on to become the 2nd largest producer of PPE in just 60 days. Although the current situation of emergency forced this, it stands as a testimony to what well-coordinated implementation of objectives can achieve. Despite facing difficulties such as lack of technical expertise, insufficient infrastructure, India has managed to considerably improve the quality of the PPEs produced in the past few months. All this has been achieved amidst the world’s strictest lockdown, and in time, most of the global supply chains are disrupted.
Various predictions and experiences from China suggest that even after the flattening of the infections curve, the emergence of mini hotspots now and then is expected around the world. Therefore, there will be a fair demand for PPEs in the future. Also, increased awareness regarding the safety norms will generate demand for the PPEs and masks in the future. Therefore, it is a golden opportunity for India to emerge as a PPE hub for the world. Although most of these pieces of equipment have been put for domestic use, India is all set to export these pieces of equipment.
Some initiatives taken by the Government
New Delhi has taken a liberal and transparent policy stand in FDI (Foreign direct investment). 100% FDI is allowed under the automatic route to the extent that it does not require prior approval by the Government of India or the RBI. Ministry of textiles has set up an FDI cell to assist, sort out operational problems, maintain data pertaining to domestic textile production, and attract FDI.
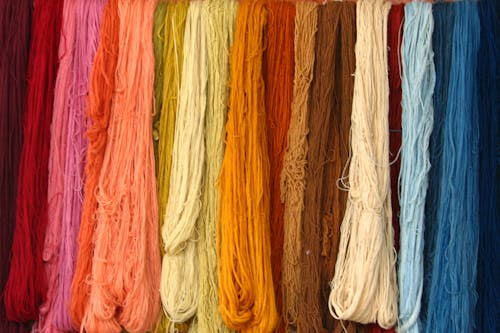
National Technical Textile Mission
Technical textiles are the textiles used for a specific purpose (e.g., fire suits, protective suits, bomb diffusing suits, military suits, etc.). They require sophisticated infrastructure and textile resources. India imports almost all the technical textiles (worth $16 billion).
The national technical textile mission was introduced in the budget this year to foster research, innovation, development, production and export promotion in this field, allocating Rs.1480 Crore in this project.
- Primary support will be provided to the manufacturers by the government for the first few years.
- The government has also abolished anti-dumping duties on PTA (purified terephthalic acid) which is an essential ingredient in the production of these textiles.
- However, this has generated dissatisfaction among the local producers of PTA such as RIL and OIL.
— Avichal Agrawal & Bipul